Cicoil Cable vs The Challengers
Extruded Flat Cables
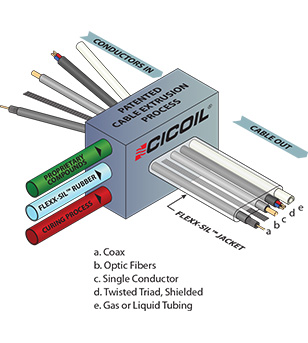
- Extruded in continuous lengths
- Automated, climate controlled process
- Easy setup of wide variety of cable and tubing
- Flexx-Sil™ jacket is produced with complete integrity and without any breaches through the encapsulation
- Cable shape customizable and infinitely repeatable
Molded Flat Cables
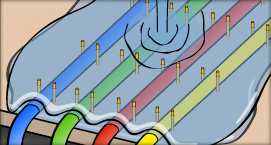
1. | Wires are stretched between pins in a mold, and then liquid silicone is poured over the wires. |
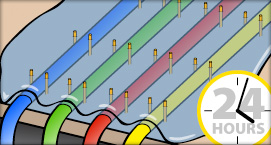
2. | Multiple pours are needed to get proper thickness, and the molded cable takes 24-48 hours to fully cure. |
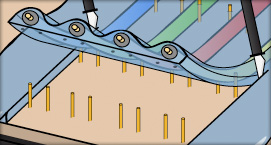
3. | The cured cable is cut out of the mold, leaving sharp edges and multiple holes. |
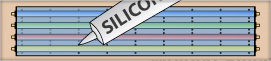
4. | The holes are filled in by hand, and the cable needs to be cured again. |
Take a look below at the Tale of the Tape. Cicoil Extruded Flexx-Sil™ Flat Cable is The Clear Winner!
Extruded Flat Cables
Molded Flat Cables
QUALITY
Cable thickness precisely controlled to within .005″, and conductor spacing accuracy to within .002″.
Large variation in thickness, and inaccurate conductor spacing. Gravity causes molded cables to be thicker at the bottom, and thinner at the top. Thickness will vary throughout the length of the cable.
Computer-controlled extrusion process means entire cable exactly the same.
Manual pouring and curing method means each cable will be unique, and there will be large variations among different cable batches.
Continuous cable lengths, as long as needed
Limited by physical mold, usually no longer than 6 feet
Extruded cable cured continuously, with no debris or material contamination.
Molded cables take many hours to fully cure. While curing, the gooey cable will collect dust, metal chips, and other airborne debris.
STRENGTH & RELIABILITY
Cable is solid, one-piece construction, due to the continuous extrusion process.
‘Bed of Nails’ in tool leaves many holes in cable when pulled from the mold. These holes are then filled by hand, and the cable is cured again, resulting in a weaker cable construction.
Cicoil cables have rounded radiuses on each end, making them stronger and also more flexible.
Molded cables are cut from the mold with Exacto blades, resulting in sharp, square edges. This greatly lessens the strength and the flexibility of the cable.
VERSATILITY & COST
Virtually any outside cable profile can be created, exactly as the application requires.
Manual pouring process does not allow complex or variations in profile, as the molding material will conform to the shape of the conductors.
Wide variety of wire conductors, tubing, mounting strip, even fiber optics can be easily incorporated into the cable.
Conductor variation is limited, and tubing, fiber optics, etc., are not available.
Quickly and easily make new cables, only $250 tooling cost.
Expensive tooling for new cables, with long lead times.
Summary
The results are clear: Cicoil's extrusion technology is the modern, automated way to produce high quality flat cables. The old fashioned method of hand pouring liquid to make molded cables is inefficient, inconsistent, and results in a lower quality flat cable.