Cicoil Flat Cable vs The Challengers
Extruded Flexx-Sil™ Flat Cables
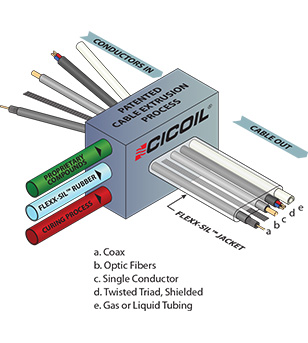
- Patented Cicoil process
- Flat cables are extruded in continuous lengths
- Automated, climate controlled process
- Easy setup of wide variety of flat cables
- Patented Flexx-Sil™ rubber jacket has complete integrity, totally surrounding the cable elements in a durable one-piece construction
- Cable shape customizable and infinitely repeatable
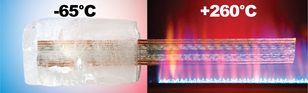
- -104°C to +260°C (-85°F to +500°F). Our flat cable temperature capability exceeds even specialized PTFE jacketed cables.
PTFE Flat Cables
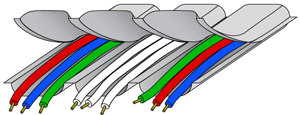
1. | 2-Piece Contruction: Two PTFE shell halves are bonded together to produce the flat cable jacket for the enclosed wires. |
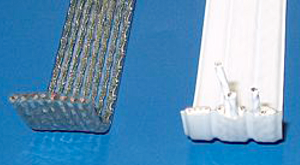
2. | Loose Wires: Wires are loose inside the two-piece cable jackets, rubbing against each during flexing cycles, and requiring clamping devices to hold in place. |
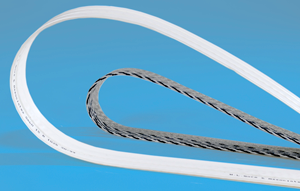
3. | High Stiffness: PTFE jacketing is fairly stiff, resulting in less flexibility and higher bend radiuses than highly flexible Flexx-Sil™ rubber. Image above show the greater natural flexiblity of Cicoil extruded Flexx-Sil™ encapsulated flat cable. |
4. | Limited Variation. Manufacturing process to produce two-piece PTFE flat cables results in a limited number of variations, and limited cable widths and lengths. |
Take a look below at the Tale of the Tape. Cicoil Extruded Flexx-Sil™ Flat Cable is The Clear Winner!
Extruded Flat Cables
PTFE Flat Cables
STRENGTH & PERFORMANCE
Cable is solid, one-piece construction, due to the continuous extrusion process.
Two-piece construction is an inherent weakness, as cable bonding is more likely to separate during operation, flexing, or under exposure to heat, cold, and/or chemicals.
Each element in Cicoil flat cables are completely surrounded by Flexx-Sil™ rubber, ensuring that they do not rub against each other and wear during operation.
Conductors are loose inside the cable halves, which can lead to premature wear as they rub together during operation.
Flexx-Sil™ rubber is naturally much more flexible than PTFE, allowing tighter bend radiuses and longer flex life.
PTFE is stiff, requiring larger bend radiuses, which takes up more space and limits flex life.
Cicoil flat cables handle extreme heat and cold. See cables resist a blowtorch, and remain flexible at -100 degrees.
PTFE cables burn and melt under exposure to fire, and become very stiff and crack in extremely cold temperatures.
Flexx-Sil™ jacketing is ‘self-healing’ from small punctures, and cable damage can easily be repaired in the field.
Any damage to PTFE shell can’t be repaired, necessitating a new replacement cable.
VERSATILITY & COST
Virtually any outside cable profile can be created, exactly as the application requires.
Pre-formed PTFE shells limit the cable profile and design.
Wide variety of wire conductors, tubing, mounting strip, even fiber optics can be easily incorporated into the cable.
Existing cable shells limit the variety of conductors, and range of sizes, that can be incorporated into a single cable.
Flat cable conductors are completely surrounded by Flexx-Sil™ rubber, requiring limited clamping.
Loose wires require extensive clamping, adding weight, inertia, and cost to overall cable.
Quickly and easily make new cables, virtually unlimited in width and length. New cables require only 100 foot minimum, and a small tooling cost.
Existing cable shells limit cable width and length. For new cable designs, there are often high minimums and/or tooling costs.
Summary
The results are clear: Cicoil's patented extrusion technology is the modern, automated way to produce high quality flat cables and flat cable assemblies. PTFE flat cables are limited in reliability and performance, while often resulting in higher design and equipment costs.